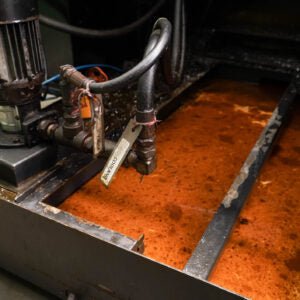
In the world of precision manufacturing, CNC machines are indispensable tools for creating complex and precise components. These machines are essential in various industries and their performance relies heavily on the proper maintenance of their components, one of which is the coolant system. Neglecting the cleanliness and quality of the coolant in CNC machines can have serious detrimental effects on both the machines themselves and the production process. Dive into the importance of maintaining clean coolant, the consequences of neglecting this crucial aspect of CNC machine maintenance, and how a CECOR Sump Cleaner can help with maintenance.
Coolant serves as a vital component in CNC machining.
It has several essential functions:
- Temperature Control: CNC machines generate a significant amount of heat during the machining process. Coolant helps dissipate this heat, preventing excessive temperatures that could cause damage to machine components.
- Lubrication: Coolant acts as a lubricant for moving parts, reducing friction and wear. This extends the lifespan of critical machine components such as bearings and slides.
- Chip Removal: During machining, chips and debris are generated. Coolant helps flush these chips away from the cutting area, preventing them from interfering with the cutting tool and workpiece.
- Surface Finish: Proper coolant application can improve the surface finish of machined parts, ensuring the desired precision and quality of the final product.
There are also several detrimental effects of dirty coolant.
- Reduced Machine Performance: Dirty coolant can lead to inefficient heat dissipation. This can cause CNC machines to overheat, leading to thermal expansion, misalignment, and ultimately, reduced precision and performance. Additionally, as coolant loses its lubricating properties due to contamination, it can result in increased wear and tear on machine components, affecting their lifespan.
- Decreased Tool Life: Contaminated coolant can accelerate tool wear. As cutting tools become dull more quickly, they require frequent replacements, increasing production costs and downtime.
- Poor Surface Finish: Dirty coolant may introduce impurities and particles into the machining process, leading to imperfections on the workpiece's surface. This can result in scrapped or reworked parts, wasting both time and resources.
- Health and Environmental Hazards: Neglected coolant can become a breeding ground for harmful bacteria and fungi. Exposure to these contaminants can pose health risks to machine operators and maintenance personnel. Additionally, improperly disposed of contaminated coolant can harm the environment.
- Increased Maintenance Costs: Regular maintenance and cleaning of coolant systems are necessary to ensure optimal performance. Neglecting this upkeep can lead to costly repairs and replacements of machine components, driving up maintenance expenses.
Consider implementing the following best practices:
- Regular Maintenance: Schedule routine coolant system maintenance, including filtration, cleaning, and replenishment of coolant fluid. This prevents the buildup of contaminants and ensures the coolant's effectiveness.
- Monitoring and Testing: Regularly monitor the condition of the coolant using testing equipment to assess its cleanliness and quality. Three important areas to monitor are concentration, pH level, and tramp oil accumulation. Address any issues promptly to prevent them from worsening.
- Proper Filtration: Invest in high-quality filtration systems to remove contaminants from the coolant. Proper filtration can significantly extend the life of both the coolant and machine components. To get ahead of the game, use a CECOR Sump Cleaner to effectively remove and filter coolant from the chips and sludge.
- Operator Training: Ensure that machine operators are trained in coolant system maintenance and understand the importance of clean coolant. Encourage them to report any issues promptly.
- Environmentally Responsible Disposal: Dispose of used coolant in compliance with environmental regulations to prevent harm to the environment. With the discharge valve on the CECOR Sump Cleaner, you are not only able to dispose of used coolant, but you can reuse coolant after it has been filtered from the chips and sludge.
CECOR is passionate about maintaining clean coolant in CNC machines which is a critical aspect of precision manufacturing. Dirty coolant can lead to reduced machine performance, increased tool wear, poor surface finish, health hazards, and higher maintenance costs. To ensure the longevity and efficiency of CNC machines and maintain the quality of production, it is imperative to prioritize coolant system maintenance and cleanliness. A great way to combat the detrimental effects of dirty coolant is by using a CECOR Sump Cleaner to clean dirty sumps. By doing so, manufacturers can safeguard their investments and optimize their CNC machining processes for better, more reliable results.
Start Your Sump Cleaner Journey